For beverage makers here in Vermont, keeping expenses low while maintaining quality is critical to success. When process heating accounts for roughly 60% of your energy consumption in beverage manufacturing, energy efficiency is a critical tool in getting ahead.
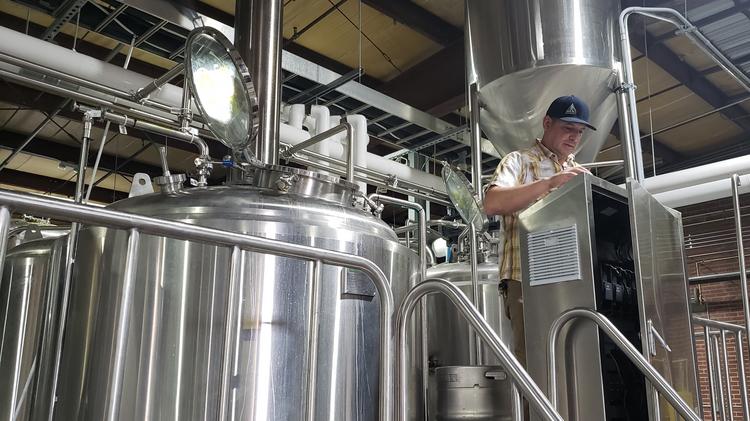
Citizen Cider is saving about $19,600 per year after they installed modulating burner controls, process water heaters, and insulation.
Boiler Maintenance
Implementing a simple maintenance program that ensures all components of your boiler are operating at peak performance can save you a significant amount of money. In the absence of such a program, your steam system could lose 10-20% of its initial efficiency in just 2-3 years.
Improved Process Controls
Flue gas monitors can give you a clear picture of the composition of your boiler’s exhaust, ensuring the right balance of excess oxygen and other products of combustion, as well as an ideal operating temperature. This makes it possible for you to optimize your fuel-to-air mixture for a flame temperature that’s efficient and produces lower emissions.
Flue Gas Heat Recovery
Adding a heat recovery system that can preheat your boiler feed water in an economizer or boiler intake air will boost your company’s energy efficiency. Generally speaking, you’ll cut your natural gas use by 1% for every 40°-50°F that you reduce your exhaust gas temperature, a move that will often pay for itself in less than five years.
Blowdown Steam Recovery
When you blow down the water from your high pressure tank to remove impurities, the pressure reduction also produces significant amounts of steam. While this steam is generally low grade, it can be used for other applications around your facility, such as space heating or feed water preheating. Introducing such a measure can save you 1–2% of your fuel costs, with an estimated payback of less than four years.
Steam Trap Inspection & Maintenance
If your steam system hasn’t been maintained in 3-5 years, it’s possible that between 15-30% of your traps will have failed, allowing live steam to escape into your condensate return system and causing significant steam loss and wasted energy. A regular maintenance program can save you up to 10% of your thermal energy costs and increase the useful output of your steam system.
Condensate Return
You can save about 10% of your energy costs by installing a condensate return system. These systems also substantially reduce the amount of chemicals you need to purchase to treat your boiler feed water. Another option to consider is using a heat exchanger to recover the heat from condensate that isn’t fit for recirculation.
Steam System Insulation
According to the U.S. Department of Energy, you can save an average of 3-13% of your energy costs by installing better insulation on your steam distribution system, which offers an average payback of less than two years. VGS can help you determine the best course of action to maximize your savings and minimize your energy use.